1.在每一权通句硫化机地沟支管道的阀门前端增加1个缓冲罐
缓冲罐罐体材料可选用Y108mX10mm的厚壁无缝钢管,罐忆长200 mn, 两端焊5 um厚的钢板。硫化排水时,尚速水流首先冲击缓冲罐壁,打在罐上向四周飞溅,在缓冲罐上部飞溅几次劝能消耗后落在缓冲罐底部,在重力的作用下,缓缓流向地沟支答。这样即把原先冲刷地沟文管的高速水流转移到缓冲端上。这种缓冲锤成木较低,至少可用3-4年,H易于更换,即只要关闭单台殖化机进地沟支管的阀门,拆卸螺栓, 10~20 min就可以换好。
2.调整硫化热水回收时间
采用缓冲后出从根本上解决了动力水排术,抽真空排水、总并管排水高道水流对地沟支管的户刷问题,但解决不了冷却水排水高速水流对地沟支管的冲刷问题。在T.1.-B1320/2895X2双模硫化机排水管道上安装缓冲罐后的试验过程中,我们发现在轮胎能化程序热水回收结京后进冷却水时,前1分多钟排出的冷却水仍然以高連流冲刷着地沟支管,而1分多钟后才变成缓缓的水流,经分析后认为是二次蒸汽造成的。在轮胎硫化程序中有一个热水回收租序,收置这个热水回收程序的目的是将硫化咬囊中的170~190"C热水回收到热水除氧装置的补水罐中,以节省能源。然而,无论硫化工艺采用的是燕汽推热水。还是直接采用冷却水推热水,一般都不能将胶囊中的热水回收干净,况且胶囊本身还带有很大热量。因此,在热水回收程序结束后,冷却水进入胶囊后很快义升温;变成120~ 140C的热水,在热水从冷却水排水管排向硫化机地沟支管的过程中,其压力从约2, 0MPa降至常压,这必然要产生二次蒸发,形成蒸汽。查《石油化工装置工艺管道安装设计手册》可知,当热水压力从2.0 MPa降至常压时,每千克热水可产生0.22 kg左右的蒸汽;查《机械工厂节能设计及使用手册》可知,120一140C热水对应的饱和蒸汽的压力为0.20~ 0.35MPa(绝压)。
为了进一步弄清由二次蒸发引起的汽液混合高速流,在LL- B1320/2895X2双模硫化机冷却水回管道上装上压力表.(见图8)又做了-项试验。当冷却水循环刚开始时,1#缓冲罐压力表显示0.2MPa(表压),2#缓冲罐压力表显示0.07MPa(表压),此时排水口水流速度仍很高。经过约70s后,两压力表显示慢慢都回到零,同时排水口水流趋于平缓。:根据这项试验,我们调整了确化工艺,将LL-B1320/2895X2双模硫化机热水回收的时间由1 min改为2 min, 这样使得冷却水循环的初始温度由调整前的140C降到100C左右,由于排水温度降低了,二次蒸发造成的蒸汽量大为减小,因此冷却水经过1个缓冲罐后,水流的动能基木耗尽,缓冲罐主水口不再出现消急的水流。据此,我们分别对其它几种型号双模硫化机的热水回收时间进行了调整
3.增设倒U形弯头
在双模硫化机冷却水、动力水、抽真空排水、总排水的回水管道中增设1个倒u形弯头倒U形弯头的管顶最高点高于地沟支回水管最末端的管顶高度,其日的是使地沟支回水管始终充满水,同时也不影响管路系统正常的重力回水运行方式。因为缓冲罐到地沟支回水管的高度差为1m左右,即使回水的动能在缓冲罐中消耗完,在重力的作用下,回水从截面1流到截面2时仍形成一一个流速,根据《供暖通风设计手册》可计算出截面2处的最小流速:v2=4.47 m●s'
通过上述改善措施,取得了成效,在延长硫化管道使用寿命的同时,由于调整了硫化热水回收时间,使热能损耗得以减少。以LL-B1320/2895X2双模硫化机为例:与原硫化工艺相比,改进后每次可多回收平均温度为120C的热水93.4 kg,每天硫化22次,可减少热量损失6.07X105kJ,折合压力为1. 5MPa的蒸汽217 kg, 以每吨蒸汽为80元计算,折合17. 36元,一年运行300天,1台双模硫化机一年仅靠增加热水回收量一项就可使生产成本减少5 208元。如果再加上节省的管道维修费用和增加的开机率,实施这3种改普硫化管道的措施后节省的费用更为可观。
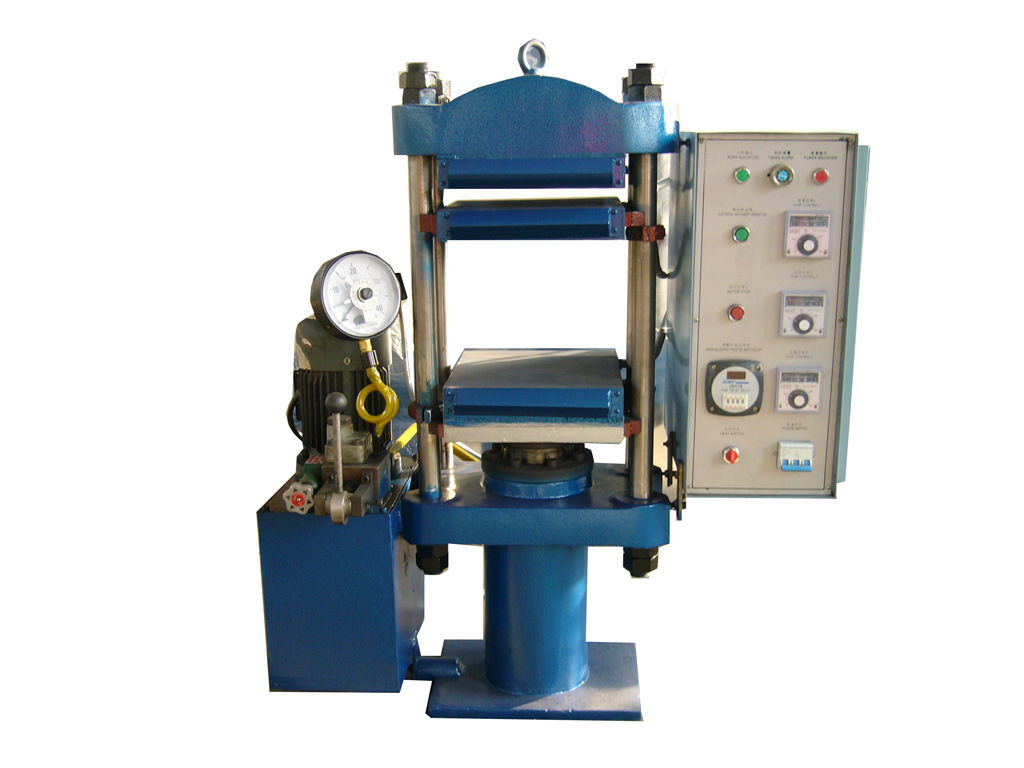